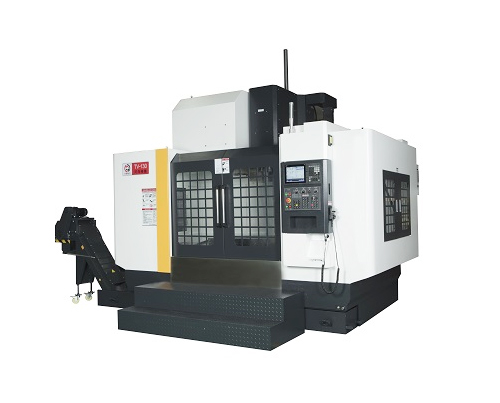
The vertical machining center is mainly used to process parts with high precision, many processes and complex shapes such as plates, discs, shells, molds, etc. It can continuously complete milling, drilling, expanding, boring and tapping in one clamping. And two-dimensional three-dimensional curved surface, accurate processing of inclined plane, the processing can be programmed, and the production cycle is shortened, so that users can obtain good economic benefits.
Function and feature description:
1 Overall layout of the machine tool
TV-130 vertical machining center adopts a vertical frame layout, the column is fixed on the machine body, the headstock moves up and down along the column (Z direction) / the carriage moves longitudinally along the bed (Y direction) / the worktable moves laterally along the carriage (X-direction) structure.
The bed, worktable, sliding seat, column, spindle box and other large parts are made of high-strength cast iron material, and the shape is resin sand process, and the stress is relieved by two aging treatments. These large parts are optimized by Pro/E and Ansys to improve the rigidity and stability of the large parts and the whole machine, and effectively suppress the deformation and vibration of the machine tool caused by cutting force. The machine body adopts Meehan sodium cast iron structure and rigid box structure design, with high rigidity and high stability.
2 Drag system
X, Y, Z axis adopts Taiwan Shangyin/Yintai high-precision, heavy-duty linear guide rail, which uses rolling instead of sliding, small friction loss, sensitive response, high positioning accuracy, X/Z axis adopts roller-lengthened six-slider design , Enhance the contact surface between the main shaft and the column casting, enhance the rigidity of the machine tool and the knob torque, the cutting feed speed is fast, the machining vibration is small, and the low speed has no crawling, which improves the precision and stability of the machine tool. Higher surface quality of the workpiece can be obtained. Due to good heat dissipation conditions, the thermal deformation of the workpiece is small, and higher machining accuracy can be obtained.
Using Japan's P4 precision grade screw special bearings, symmetrical axial and radial preloads ensure afternoon noise during high-speed continuous operation.
The three-axis adopts Taiwan C3-grade precision ball screw with preload at the end, which ensures excellent transmission accuracy and positioning accuracy.
X, Y, Z three-axis servo motors are directly connected with high-precision ball screws through elastic coupling joints, reducing intermediate links, realizing gap-free transmission, flexible feeding, accurate positioning, and high transmission precision.
The Z-axis servo motor has an automatic brake function. In the event of a power failure, the brake can automatically hold the motor tightly, but it cannot rotate, which plays a role in safety protection.......
technical parameter:
Stroke Specifications | Unit | TV-130 |
X/Y/Z axis travel | mm | 1300/700(800)/700 |
Distance from spindle nose to work table | mm | 150-850 |
Distance from spindle center to column | mm | 755(855) |
Feed | ||
Rapid feed (X/Y/Z axis) | m/min | 20/20/20 |
Cutting feed | mm/min | 1-10000 |
Feed motor power (X/Y/Z axis) | kw | 3/3/3(4.5/4.5/4.5) |
Workbench | ||
Table size (X/Y axis) | mm | 1400X700(1500X800) |
T-slot (width x number x spacing) | mm | 18X5X130(18X7X110) |
Workbench maximum load | kg | 1300 |
Spindle | ||
Spindle moving method | 一 | Belt/Gearbox |
Spindle Motor Specifications | kw | 15/18.5 |
Spindle speed | rpm | 8000(6000) |
Spindle taper hole specification | - | BT-40(BT-50) |
Precision | ||
Positioning accuracy(JIS B6228/6339) | mm | ±0.01 |
Repeatability(JIS B6228/6339) | mm | ±0.006 |
ATC | ||
Tool magazine form | - | Knife Arm |
Tool magazine capacity | - | 24 |
Maximum tool diameter/adjacent tool space | mm | Φ78/Φ120(Φ112/Φ200) |
Maximum tool length | mm | 300 |
Maximum tool weight | kg | 8(15) |
Tool change time(T-T) | sec | 2⑷ |
Other | ||
Electricity demand | kVA | 35 |
Air pressure demand | kg/cm2 | 6 |
Cutting fluid capacity | L | 280 |
Machine Weight (Approx.) | kg | 9500(11000) |
Appearance dimensions of the machine (length X width X height) | mm | Front Row 3200*4800*3800 |